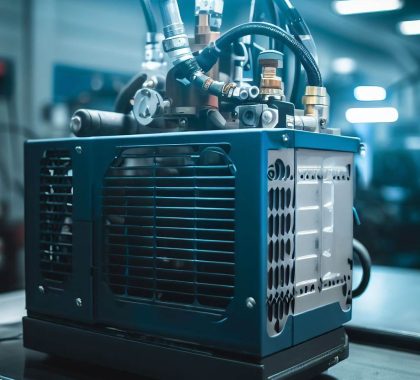
Air compressors are extensively utilized in various industries such as textile, pharmaceutical, laboratory, food processing, and electronics, serving as the third power source after electricity and water.
When selecting an appropriate air compressor for a processing line, several crucial factors must be taken into account. Making an informed decision regarding the selection of a compressor is crucial to ensure optimal efficiency of the processing line. Factors such as the required amount of compressed air flow and the size and power source of the compressor must be carefully considered.
This article aims to provide insights into the essential factors that must be taken into account while selecting an appropriate air compressor that matches the requirements of a processing line.
1. Analysis of Compressed Air Flow
One of the critical considerations in selecting an air compressor for a processing line is the volume of compressed air flow needed. The determination of the necessary air pressure is contingent upon various factors, such as the dimensions and category of the processing equipment utilized.
In order to guarantee the selection of an appropriate compressor capable of providing the required volume of airflow, it is imperative to conduct an assessment of the equipment and ascertain the precise specifications. Typically, the process involves quantifying the required flow rate of air and the corresponding pressure to make an informed decision on the appropriate compressor that can fulfill these specifications.
2. The Determination of Compressor Size
The dimensions of the compressor unit constitute a crucial aspect to contemplate while selecting a compatible air compressor for a production line. The determination of the appropriate compressed air system for a facility is contingent upon various factors, such as the facility’s size and the required volume of compressed air flow.
In general, it is advisable to select a compressor that is compact yet capable of providing the required volume of compressed air flow. This approach can potentially reduce the energy consumption needed to operate the compressor while ensuring that the processing line receives the required level of air pressure.
3. Energy Source
The selection of an appropriate air compressor for a processing line requires careful consideration of the power source that will be utilized. A variety of power sources are available for selection, such as electric, gasoline, diesel, and propane.
The selection of an optimal power source for a facility is contingent upon various factors such as cost, availability, and environmental considerations. For instance, the selection of electric compressors could be a judicious option for those seeking an energy-efficient solution. Conversely, gasoline or diesel-powered compressors may be more suitable for individuals operating in a remote location where access to electricity is restricted.
4. The selection of an appropriate air compressor for a processing line is a critical consideration, with efficiency being a primary concern. Apart from the reduction of energy expenses, the selection of an efficient compressor can also aid in the minimization of downtime and the reduction of maintenance needs.
Among the compressor options available, oil-free compressors and variable-speed compressors are considered to be highly efficient. These compressors are engineered to function with greater efficiency compared to conventional reciprocating or rotary screw compressors, with a primary emphasis on decreasing energy consumption and minimizing maintenance needs.
5. Maintenance refers to the process of ensuring the proper functioning and upkeep of equipment, machinery, or infrastructure. It involves regular inspections, repairs, and replacements of parts to prevent breakdowns and prolong the lifespan of the assets.
The maintenance prerequisites of an air compressor are essential aspects to contemplate while selecting a compatible air compressor for your processing line. Ideally, the selection of a compressor should prioritize ease of maintenance and minimal downtime for repairs.
Several factors must be taken into account regarding maintenance, such as the quantity of lubrication needed, the frequency of filter replacements, and any particular cleaning or maintenance obligations that may arise. By assessing these variables and selecting a compressor that is engineered for effortless maintenance, one can minimize downtime and guarantee the seamless and efficient operation of the processing line.
Further Factors to be Taken into Account
Apart from the aforementioned considerations, there exist several other factors that necessitate attention while choosing an appropriate air compressor that matches a processing line. The following items are encompassed within this category:
The noise level of the compressor may need to be taken into consideration based on the processing line’s location and the type of equipment being utilized. Certain types of compressors are engineered to function with reduced noise levels compared to others. This feature can prove to be fundamental in scenarios where the compressor is being utilized in a residential locality or any other setting that is sensitive to noise pollution.
The consideration of installation requirements for a compressor is also significant. It is advisable to select a compressor that facilitates easy installation and seamless integration into the current processing line with minimal interference.
The environmental impact of the compressor may need to be taken into account, depending on the facility and processing line location. It is imperative to select a compressor that is tailored to function in the particular setting and has the potential to reduce the carbon footprint.
In conclusion, it can be inferred that selecting an appropriate air compressor that aligns with a processing line is a key decision that can significantly influence the overall effectiveness and output of your establishment. By meticulously evaluating variables such as compressed air flow, compressor dimensions, power supply, efficacy, and maintenance prerequisites, along with any other pertinent factors that may be relevant to your particular circumstances, you can make a well-informed determination regarding the most suitable compressor for your processing line. For more information about how to do a system-wide energy-saving, please refer to my another blog.
Johnny Wayne