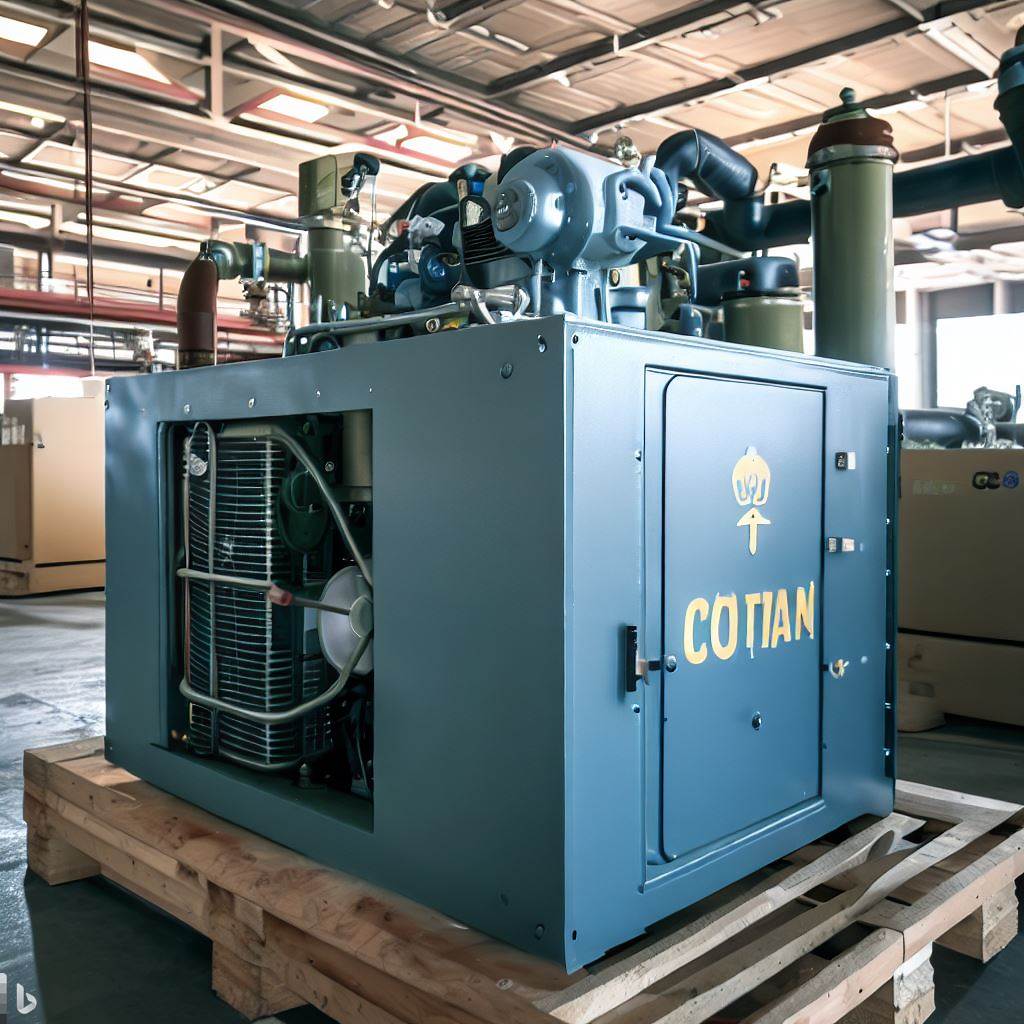
As one of the indispensable equipment in industrial production, the operating status of the air compressor is directly related to the production efficiency and economic benefits of enterprises. However, the air compressor faces various challenges during operation, such as high energy consumption, frequent failures, and high maintenance costs. Therefore, it is crucial to formulate scientific and reasonable air compressor management strategies. This article will conduct a professional, comprehensive, and original in – depth discussion on air compressor management from the following aspects:
I. Clarify the Management Objectives of the Air Compressor
Before discussing specific management strategies, it is first necessary to clarify the management objectives of the air compressor:
1. Ensure the Safe and Stable Operation of the Equipment
- Prevent and reduce the occurrence of failures and avoid production interruptions caused by equipment failures.
- Timely detect and eliminate potential safety hazards to ensure the safety of equipment and personnel.
2. Improve the Operating Efficiency of the Equipment
- Optimize the operating parameters of the air compressor, reduce energy consumption, and improve the output efficiency of compressed air.
- Reduce unnecessary idling operation time and improve equipment utilization.
3. Prolong the Service Life of the Equipment
- Develop a scientific maintenance plan to extend the overhaul cycle and service life of the equipment.
- Reduce equipment depreciation costs and improve the return on investment.
4. Reduce Operating and Maintenance Costs
- Reduce energy consumption and lower operating costs.
- Reduce the frequency of maintenance and the consumption of spare parts, and control maintenance costs.
5. Achieve Intelligent Management
- Introduce advanced monitoring and control technologies to achieve remote monitoring and intelligent management of the air compressor.
- Collect and analyze operating data to provide a basis for optimizing operating strategies.
II. Establish a Complete Equipment File
A complete equipment file is the basis for air compressor management and includes:
1. Basic Equipment Information
- Equipment model, specifications, manufacturer, date of manufacture, installation location, etc.
- Documents such as equipment purchase contracts, technical agreements, and acceptance reports.
2. Technical Information
- Equipment operation manuals, electrical schematic diagrams, pipeline layout diagrams, etc.
- Equipment design parameters, performance curves, operation and maintenance manuals, etc.
3. Operation Records
- Equipment operation time, start – stop time, operating status, etc.
- Operating parameters of compressed air, such as production volume, pressure, temperature, flow rate, etc.
- Equipment energy consumption records, including power consumption, cooling water consumption, etc.
4. Maintenance Records
- Information on daily maintenance content, time, personnel, etc.
- Regular maintenance plans, maintenance content, maintenance personnel, maintenance results, etc.
- Equipment failure records, including failure occurrence time, phenomena, causes, handling measures, etc.
5. Spare Parts Management
- Spare parts list, including information such as name, model, specifications, quantity, etc.
- Spare parts purchase records, inventory information, requisition records, etc.
III. Develop a Scientific Maintenance Plan
Scientific maintenance is the key to ensuring the stable operation of the air compressor. The following maintenance plans should be developed according to the equipment operation status and manufacturer’s recommendations:
1. Daily Maintenance
- Regularly check the equipment appearance, lubrication, sealing, etc.
- Clean the equipment surface and cooler fins to maintain good heat dissipation conditions.
- Check whether the operating parameters such as oil level, water level, pressure, and temperature are normal.
- Listen to the equipment operation sound and promptly detect abnormal noises.
2. Regular Maintenance
- Regularly replace vulnerable parts such as lubricating oil, filters, and oil separation cores.
- Regularly clean components such as coolers and filters to prevent blockage.
- Check and tighten the bolts at all connection parts of the equipment to prevent loosening.
- Conduct a comprehensive performance test and calibration of the equipment to ensure that all parameters meet the requirements.
3. Preventive Maintenance
- Use advanced technologies for data analysis, such as vibration analysis, lubricating oil analysis, temperature and pressure analysis, etc., to monitor the equipment status.
- Based on the monitoring results, discover potential failure hazards in advance and take corresponding preventive measures.
- For example, when abnormal bearing vibration is monitored, the bearing can be replaced in a timely manner to avoid equipment shutdown caused by bearing damage.
4. Overhaul
- When the equipment has been in operation for a certain period or a major failure occurs, an overhaul is required.
- The overhaul content includes fully disassembling, cleaning, inspecting, replacing worn – out parts, and repairing damaged parts of the equipment.
- After the overhaul, the equipment should be debugged and its performance tested to ensure that the equipment returns to the optimal operating state.
IV. Optimize the Operating Parameters of the Air Compressor
Reasonable setting of operating parameters can effectively reduce energy consumption and improve the operating efficiency of the equipment:
1. Pressure Setting
- According to the production process requirements, reasonably set the output pressure of the air compressor to avoid energy waste caused by excessive pressure.
- For example, for general industrial applications, the compressed air pressure controlled at 0.6 – 0.8MPa can meet the requirements.
2. Air Discharge Volume Adjustment
- Adjust the air discharge volume of the air compressor in a timely manner according to the change in air consumption to avoid the equipment operating at a low – load state for a long time.
- Frequency conversion speed – regulation technology can be adopted to adjust the motor speed in real – time according to the air consumption to achieve continuous adjustment of the air discharge volume.
3. Cooling System
- Regularly check the parameters of the cooling water, such as water quality, water temperature, water pressure, etc., to ensure the normal operation of the cooling system.
- Regularly clean the cooler to prevent the cooler from scaling and affecting the heat dissipation effect.
- Reasonably control the cooling water flow rate to avoid energy waste caused by excessive cooling water flow.
4. Control System
- Regularly calibrate control elements such as pressure sensors and temperature sensors to ensure the accuracy of the control system.
- Optimize the control program to achieve functions such as automatic start – stop, loading and unloading, and pressure adjustment of the air compressor, and improve the degree of equipment automation.
V. Strengthen Spare Parts Management
Spare parts management is an important part of air compressor management:
1. Spare Parts Inventory Management
- Develop a reasonable spare parts inventory plan according to the equipment operation status and spare parts consumption.
- Avoid excessive spare parts inventory occupying funds or insufficient inventory affecting equipment maintenance.
2. Spare Parts Procurement
- Select reliable and reasonably – priced spare parts suppliers.
- Regularly evaluate spare parts suppliers to ensure the quality of spare parts.
3. Spare Parts Usage
- Establish a spare parts requisition system and standardize the spare parts usage process.
- Strengthen the tracking management of spare parts usage and promptly discover and solve spare parts quality problems.
VI. Introduce Intelligent Management Technologies
With the development of technologies such as the Internet of Things, big data, and artificial intelligence, intelligent management has become the development direction of air compressor management:
1. Remote Monitoring
- Use the Internet of Things technology to achieve remote real – time monitoring of the air compressor.
- Information such as equipment operating status, operating parameters, and fault alarms can be viewed anytime and anywhere through mobile APPs or computer terminals.
2. Data Analysis
- Collect equipment operating data and conduct big data analysis.
- Analyze equipment energy consumption trends, failure occurrence laws, operating efficiency, etc., to provide a basis for optimizing equipment operating strategies.
3. Predictive Maintenance
- Use artificial intelligence technology to predict equipment failures.
- Based on equipment operating data, predict potential equipment failures in advance and take timely preventive measures.
4. Intelligent Control
- Introduce artificial intelligence algorithms to achieve intelligent control of the air compressor.
- According to parameters such as changes in air consumption and pressure fluctuations, automatically adjust the equipment operating parameters to achieve energy conservation and consumption reduction.
VII. Personnel Training and Safety Management
1. Personnel Training
- Regularly train operators to improve their operation skills and equipment maintenance knowledge.
- The training content includes equipment operation procedures, common fault handling methods, emergency handling measures, etc.
2. Safety Management
- Establish a sound safety management system and clarify the safety responsibilities of personnel at all levels.
- Regularly conduct safety inspections of the equipment to promptly discover and eliminate potential safety hazards.
- Develop emergency plans and organize drills regularly to improve the ability of staff to respond to emergencies.
Air compressor management is a systematic project that needs to start from multiple aspects, such as establishing equipment files, formulating maintenance plans, optimizing operating parameters, spare parts management, application of intelligent technologies, and personnel training and safety management. Only by continuously optimizing management strategies can the operating efficiency of the air compressor be improved, operating and maintenance costs be reduced, the service life of the equipment be extended, and greater economic benefits be created for enterprises.